Maximising flexibility in multi-layered cascades: aventron's journey to price-driven dispatch with HYDROGRID
aventron, a leading Swiss producer of renewable energy, partnered with HYDROGRID to optimize the use of water in their Nordic hydropower plant fleet. This case study highlights how automated, digitally optimized production planning can enhance storage flexibility and enable flexible dispatch, ultimately maximizing efficiency and profitability.
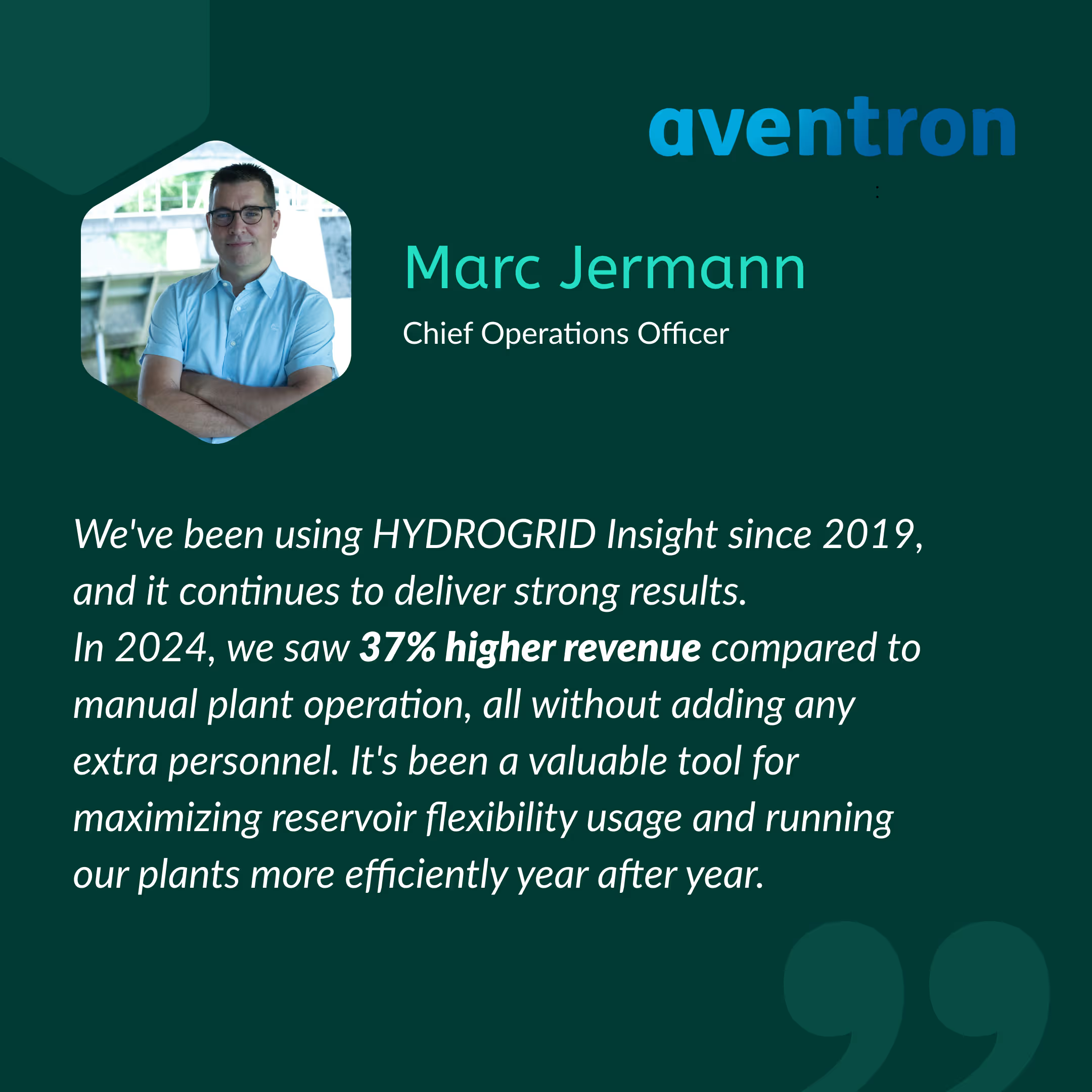
Key Highlights
- Proactive Leadership: aventron demonstrated industry foresight by implementing machine learning technology in daily price-driven dispatch operations, improving efficiency sustainably through innovative technologies.
- Strategic Implementation: The team at aventron integrated HYDROGRID Insight with their existing infrastructure seamlessly, making the best of available technology for their specific needs, without compromising their existing setup.
- Impressive Results: This proactive approach resulted in significant improvements in operational efficiency and cost savings, earning aventron progressively better financial results year-on-year, with the latest reports showing a 37% increase in revenue in 2024, when compared to non-optimized operations.
- Seasonal Readiness: The new water management approach, powered by tailored inflow forecasting, helped aventron prevent icing in winter and prepare for snowmelt in late spring in the Nordic climate.
Background
aventron's hydropower portfolio in Norway includes a diverse range of small-scale hydropower plants. The portfolio is designed to leverage Norway's natural resources and geographical advantages, ensuring efficient and sustainable energy production. This strategic approach allows aventron to maximize the potential of its hydropower assets while contributing to Norway's renewable energy goals, all without added operational effort.
Norwegian weather poses specific challenges in hydropower operations. The impact of snowmelt and ice significantly affects inflow forecasting. During spring, snowmelt increases water inflow, while ice formation in winter can restrict water flow and turbine operations. Accurate inflow forecasting is essential to manage these seasonal variations and ensure efficient hydropower production.
Challenges

The primary challenge faced by aventron was managing the small intake capacities which are quite common in Nordic projects,while ensuring optimal water usage. One example of constrictive conditions is the Boge project for which the limited storage in the intake dam made it difficult to maintain consistent turbine operation, leading to inefficiencies and potential revenue loss.
The Boge cascade system is divided into two levels: Boge 1 and Boge 2. Boge 1 - the first reservoir in the cascade chain- has a reservoir capacity of 0.38 hm³, while Boge 2 is an intake with a much smaller capacity of 0.01 hm³. This limited storage capacity restricts operations upstream. Additionally, the smaller intake size at Boge 2 makes it more susceptible to freezing, further complicating water management and turbine operations during colder months. Turbine throughput of the Boge cascade sistem introduces another layer of complexity to operations: Boge 1, with a turbine throughput of 0.6 m³/s, benefits from the larger reservoir but limited throughput at gate level, when compared with Boge 2.
Even for cascades such as Boge, aventron explored the opportunity of price drive dispatch operations using the existing storage flexibility at the top reservoir level. Here's how they did it and the results they achieved with no additional operational cost dedicated to Boge.
Solution
{{challenges-section}}
HYDROGRID implemented an automated, digitally optimized production planning system to address these challenges. The system focused on:
- Optimizing Water Usage: By carefully managing the water flow from the Boge upper reservoir to the intake dam, the system ensured that the turbines operated at their optimal throughput. This approach maximized the efficiency of water usage, even with the small intake capacities.
- Enhancing Storage Flexibility: The optimized water usage freed up storage capacity in the intake dam, allowing Aventron to better manage water levels and respond to fluctuating energy demands.
- Price-Driven Dispatch: With improved storage flexibility, Aventron could leverage price-driven dispatch strategies. The system enabled the company to store water during periods of low electricity prices and release it when prices were higher, maximizing revenue.

Results
The implementation of HYDROGRID's automated production planning system led to significant improvements:
{{results-section}}
- Increased Efficiency: The optimized water usage resulted in a more consistent and efficient operation of the turbines, despite the small intake capacities.
- Enhanced Flexibility: The freed-up storage capacity allowed aventron to better manage water levels and respond to market demands.
- Maximized Revenue: By leveraging price-driven dispatch, aventron was able to capitalize on higher electricity prices, increasing overall profitability. In 2024, they saw 37% better results for the Boge project, when compared to non-optimized methods, all without adding any extra personnel.
- Reduced OpEx costs: The automated solution was able to provide 24/7 water management tailored to each site, without adding more personnel, or compromising on reactivity and efficiency.
Conclusion
aventron's partnership with HYDROGRID demonstrates the potential of automated, digitally optimized production planning in the hydropower sector. By optimizing water usage and enhancing storage flexibility, aventron was able to overcome the challenges of small intake capacities and maximize their operational efficiency and revenue.
Get in touch with our hydro consultants to learn how!
Limited storage
Automated planning, optimized water usage
Freezing risk
Ice/snow pack constraint automation
Throughput bottlenecks
ML inflow forecasting tailored at each level of Boge cascade